Shipbuilding
Excellent and Reliable Solutions for Shipbuilding
Due to the unique characteristic of vessels and offshore platforms, the equipment of their electrical and electronic must be highly sustainable, reliable, and resistant to seawater, lubricating oils, fuels, moisture, rat-bite, high temperature (84ºC,flame retardant in 15 minutes ). To adopt high quality insulating materials, professional fixing methods, well designed cable protection, and fully identification will ensure safety and reliability of electronic control system. As well as it will make maintenance easier.
Facing the competition of global market, the margin of marine industries has been beaten down, and the lengthy period of construction becomes heavy burden for shipyards. Hua Wei provides high quality, better cost-performance values of stainless steel ties and wiring accessories, designs and keeps improving products’ functions which highly increase the efficiency of ship assembly. Through the time and labor being saved by our wiring solution, the marine industries could reduce the total cost of ship build.
Hua Wei’s high quality products comply with UL electrical components regulations, and certificated for type approval of shipbuilding industry by ABS, DNV GL, and BV, which are compliant or exceed industrial standards. Hua Wei’s most endurable and reliable performance of wiring solutions is the best choice for marine industries.
- Safety: Improper cable management can lead to short circuits, fires, or signal interruptions, posing severe threats to crew safety and equipment functionality.
- Durability: The maritime environment is characterized by high humidity, salt spray, and extreme temperature variations. Cables must be adequately protected to prevent corrosion or physical damage.
- Maintenance Efficiency: Well-organized cable layouts and secure fastening systems reduce maintenance costs, shorten inspection times, and improve vessel operational efficiency.
- Noise Reduction: Loose cables may generate noise due to vibrations, particularly on cruise ships or high-end vessels, compromising passenger comfort and equipment stability.
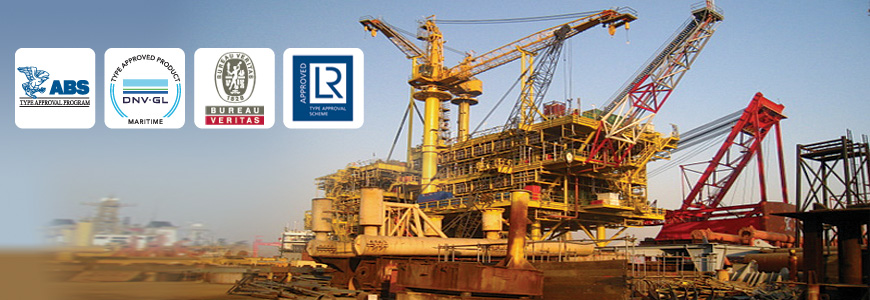
Key Considerations for Cable Management
- Vibration Resistance: Ships experience constant vibrations during sea operations. Cable fixtures must feature anti-vibration designs to prevent cables from loosening due to movement.
- Moisture and Waterproofing: Cable management components must be resistant to humidity and waterproof to withstand condensation inside the vessel and exposure to the marine environment.
- Salt Spray and Corrosion Resistance: Materials should exhibit high resistance to salt spray, particularly for cables exposed on the deck or within the engine room.
- Weight and Space Efficiency: Given the limited interior space of ships, lightweight and compact components are essential to optimize the use of available space.
- High-Temperature and Flame Resistance: Components must withstand high temperatures to prevent material degradation and include flame-retardant properties to minimize smoke and toxic hazards in case of fire.
Recommended Cable Management Components and Application Scenarios
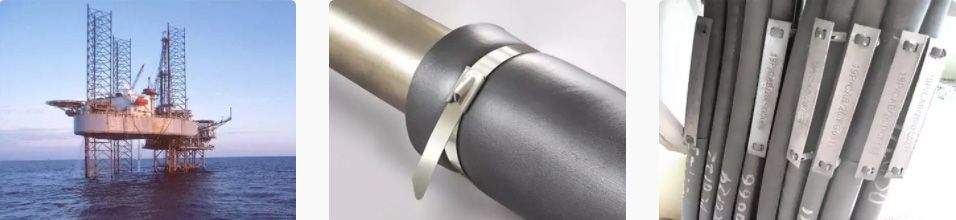
1. Stainless Steel Cable Ties
Due to the maritime environment's high humidity, salt spray, and frequent vibrations, stainless steel cable ties are indispensable for their exceptional corrosion resistance. They are particularly suited for long-term use in harsh marine conditions, such as on deck equipment, the external hull, and within engine rooms. Typically made from 304 or 316-grade stainless steel, the latter is preferred for its higher molybdenum content, offering superior resistance to salt spray and chemical corrosion. This makes 316 stainless steel cable ties ideal for extreme conditions surrounding ships.
Stainless steel cable ties must comply with the standards set by classification societies such as DNV-GL, ABS, or Lloyd’s Register to ensure durability and safety. Furthermore, these ties should pass ASTM B117 salt spray tests to validate their corrosion resistance and meet UL fire safety standards to handle high-temperature or fire-prone environments. To ensure safety, especially in interior applications, stainless steel cable ties should also possess flame-retardant properties and low smoke toxicity. This prevents the release of harmful gases in emergencies, safeguarding both crew members and onboard equipment.
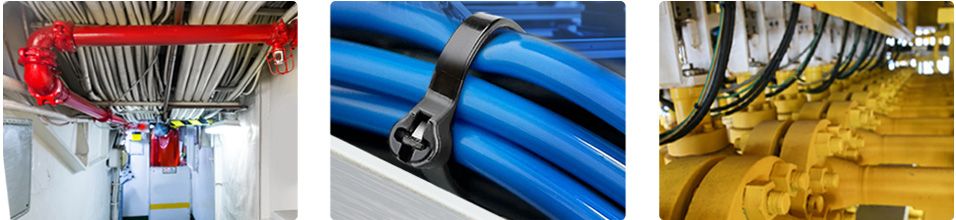
2. Steel Barb Cable Ties
Steel barb cable ties are designed to meet the demands of high-vibration, highly corrosive, and extreme environments. Their unique construction combines a lightweight, flexible nylon body with a stainless-steel barb embedded in the locking mechanism, ensuring precise locking and exceptional tensile strength. This design allows the cable tie to endure continuous vibrations during maritime operations without loosening or breaking, making it ideal for use in engine rooms, exposed deck areas, and critical internal cable management applications.
To ensure performance, steel barb cable ties must pass ASTM B117 salt spray tests, demonstrating their corrosion resistance in marine environments. They also need to comply with UL flame-retardant and low-smoke toxicity standards, particularly for interior use, to ensure safety by minimizing the release of harmful gases during a fire.
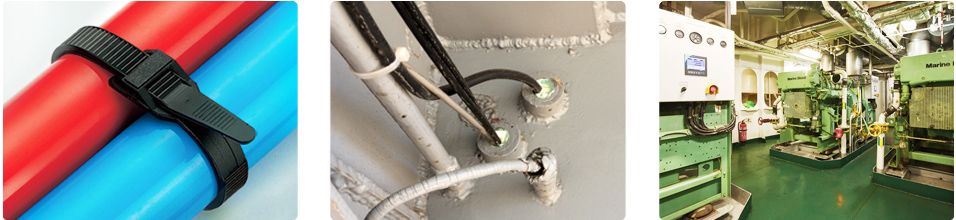
3. Low Profile Head Cable Ties
Low profile head cable ties are uniquely designed with a parallel alignment of the head and body, significantly reducing protrusions. This makes them ideal for applications in confined spaces or where minimizing interference is crucial. In maritime environments, where interior space is often limited—such as in electronic control boxes, densely packed piping areas, and engine compartments—low profile head cable ties provide efficient bundling while avoiding the installation difficulties associated with traditional, bulkier cable ties. Their compact design ensures reliable and stable fastening without compromising the surrounding structure.
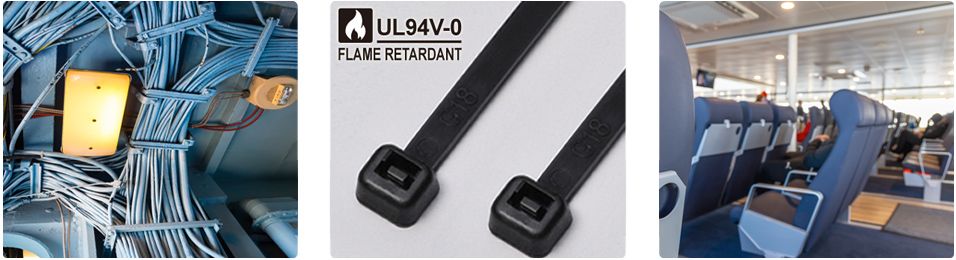
4. Flame-Retardant Cable Ties (UL94V-0 Rated)
Flame-retardant cable ties with a V-0 rating are essential in maritime environments with dense cabling and potential fire risks, especially within interior spaces or equipment clusters. These cable ties offer superior flame-retardant properties and low smoke toxicity, making them the first choice for shipboard cable management. They can effectively suppress flame spread during a fire and release minimal toxic gases during combustion, ensuring more time for evacuation and reducing fire damage.
Manufactured from high-performance nylon (e.g., PA66), these cable ties meet UL94 V-0 standards, ensuring self-extinguishing properties within 10 seconds without dripping. They also comply with classification societies like DNV-GL, ABS, or Lloyd’s Register, requiring rigorous tests for corrosion resistance, high-temperature durability, and aging resistance to ensure long-term performance in varied shipboard environments. Proper installation requires careful alignment with cables and controlled tensioning using professional tools to avoid over-tightening, which could damage cables or the tie itself.
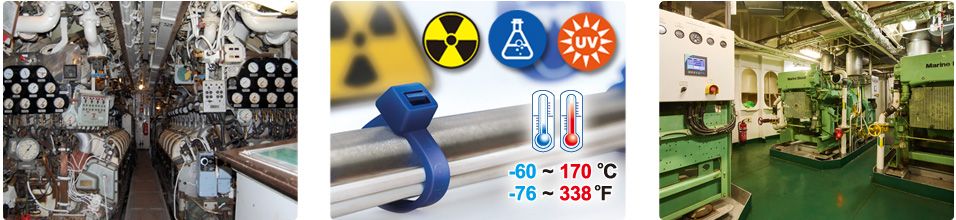
5. Tefzel® Cable Ties
The maritime industry demands cable management solutions that meet stringent environmental and regulatory requirements, particularly in response to climate change and emission standards. Future-ready ships must ensure that all cabling and wiring systems—including mounting bases, cable ties, and conduits—can withstand temperatures of approximately 150°C, particularly near new propulsion systems designed for higher combustion temperatures.
Tefzel® cable ties, made from ETFE (ethylene tetrafluoroethylene), offer exceptional heat resistance, tolerating temperatures up to 170°C. This makes them particularly suitable for high-temperature zones such as engine rooms, where heat expansion and radiation pose significant challenges to traditional materials. Additionally, their superior chemical resistance ensures protection against common shipboard elements like fuel, lubricants, and salt spray. This makes them ideal for external hull applications, chemical storage areas, and other exposed locations.
Tefzel® cable ties must meet rigorous certification standards, including UL94 V-0 for flame retardancy, ensuring self-extinguishing properties without harmful emissions during fire incidents. Their resistance to UV radiation and gamma rays further enhances their durability, ensuring stable performance even in long-term exposure to sunlight or radiation. These cable ties are widely used in engine rooms, deck equipment, and chemical storage zones, providing a robust solution for efficient ship operation and safety management.
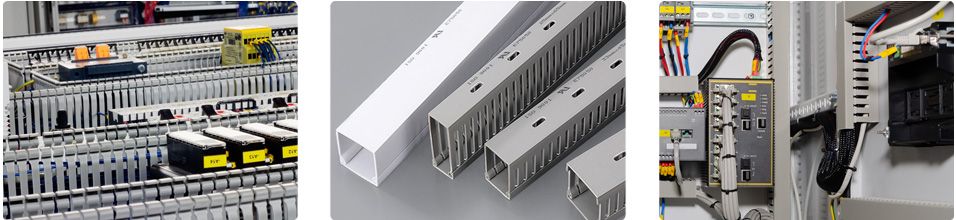
6. Wire Ducts
Wire ducts are primarily designed to protect and organize cables, preventing damage caused by wear, vibration, or external factors. They also offer electromagnetic shielding, making them essential in ship applications such as engine rooms, radar systems, control rooms, and communication systems.
In high-temperature, high-vibration environments like engine rooms, wire ducts effectively isolate heat sources and securely fasten cables, preventing disconnection due to temperature fluctuations or vibrations. For radar and communication equipment, their shielding capabilities protect against electromagnetic interference, ensuring stable data and signal transmission.
The materials and design of wire ducts must comply with various international certification standards. For maritime applications, wire ducts are typically made from high-temperature resistant and corrosion-resistant materials, such as flame-retardant nylon, which must meet stringent testing requirements like the UL94 V-0flame-retardant rating.
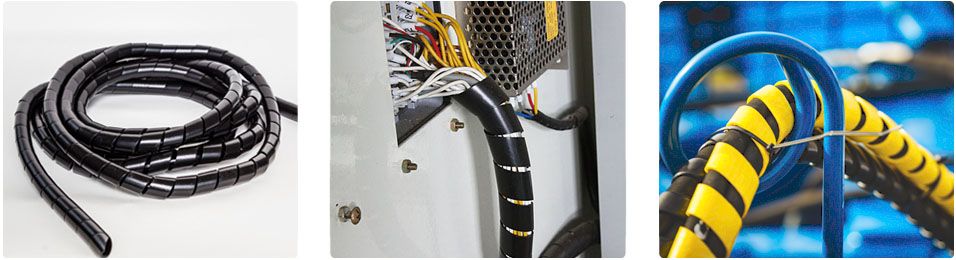
7. Spiral Wrapping Bands
Spiral Wrapping Bands are typically made from high-durability plastic materials such as polyethylene or polyester. These materials provide excellent abrasion resistance, chemical resistance, and UV protection. Their flexibility allows them to easily accommodate multiple cable layouts, making them ideal for dense cable management in electronic equipment cabinets or bundling cables in ship engine rooms and communication systems.
The spiral design enables easy installation and removal, offering exceptional convenience for future maintenance and cable adjustments.
Explore more about the features and applications of our Steel-Tooth Cable Ties , or
Contact us for additional information.
Why Choose Hua Wei?
- Over 45 years experiences in designing and manufacturing of cable ties.
- Core technology: Precise stamping and molding injection.
- Rich experience and specialty of precise molding in engineering plastic Polyamide 6,6
- Advanced molding facilities and outstanding R&D teamwork
- Our in-house molding capability allows great flexibility in production and enables us to develop products collaboration with our clients.
- Providing customize packaging design and work in process with your brand.
- Stable supply chain with on-time delivery.
Remarks: Hua Wei is a professional OEM factory, followed the MOQ for each order.
New Product
Featured product
Hot
Stainless Steel Ties
Hot
Stainless Steel Ties
With high resistance to various corrosive agents such as acids, alkali, UV, and rust, …
Read MoreHot
Wire Ducts
Hot
Wire Ducts
The premium solution for routing and hiding wires in control panels.
Read MoreHot
Standard Cable Ties
Hot
Standard Cable Ties
Available materials include heat stabilized, weather resistant and flame retardant polymers,...
Read MoreHot
(GIT-703) Cable Tie Tensioning Tool
Hot
(GIT-703) Cable Tie Tensioning Tool
The new cable tie installation tool can fasten and cut nylon cable ties quickly & safely
Read More