Transportation
Cable Management in the Transportation Industry
The transportation manufacturing sector serves as the cornerstone of the global economy, driving trade and mobility. It encompasses the design, production, and integration of vehicles and transportation systems, including automobiles, railway vehicles, airplanes, ships, and public transit systems. Its influence spans commerce, urban development, and technological innovation, making it a vital domain shaping the modern world.
![]() | With a broad supply chain that includes raw material suppliers, component manufacturers, assembly plants, and distribution networks, the transportation manufacturing industry caters to land, air, sea, and rail transport. Each mode has unique requirements and market dynamics, yet all share a focus on efficiency, safety, and sustainability. Over the past decades, the sector has undergone significant transformations. Emerging markets have become production and consumption hubs, shifting traditional manufacturing centers. The rise of global supply chains has accelerated this shift, enabling manufacturers to access diverse markets while optimizing costs. Furthermore, advancements in material science, such as lightweight composites and high-strength alloys, have revolutionized vehicle design, enhancing performance and fuel efficiency. |
Emerging Trends Reshaping Transportation Manufacturing
1.Electrification of Transportation:
Governments worldwide are driving electric vehicle (EV) adoption through subsidies and infrastructure investments. Manufacturers are expanding EV product lines and developing advanced battery technologies to extend range and reduce costs.
2.Autonomous Driving Technology:
Though still in its early stages, fully autonomous vehicles hold immense potential in logistics, public transit, and personal mobility. Companies are investing heavily in artificial intelligence and sensor technology to overcome technical challenges and regulatory hurdles.
3.Sustainability:
Beyond promoting low-emission vehicles, manufacturers are adopting circular economy principles by emphasizing recyclability and waste reduction during production. Rail and maritime transport, traditionally seen as greener options, are further enhancing their eco-friendly image with hydrogen fuel cells and energy-efficient designs.
4.Digital Integration:
Industry 4.0 principles - characterized by IoT, big data analytics, and robotics—are streamlining manufacturing processes, enabling real-time monitoring, predictive maintenance, and improved quality control. These advancements not only boost productivity but also lower operational costs, enhancing competitiveness.
Performance and Requirements of Wiring Management Materials
1.Vibration Resistance
Transportation equipment undergoes high-frequency vibrations, especially in railways, aviation, and heavy vehicles. Wiring materials must remain secure in such conditions to prevent cable loosening or damage. For example:
- EV Battery Modules: Must endure continuous vibrations and shocks during operation, particularly on rough roads or at high speeds. Wiring components must prevent connectors from loosening or failing to ensure stable power delivery and data transmission.
- Aerospace: Must handle high-frequency vibrations and acceleration forces during takeoff, landing, and flight. Components must prevent fatigue-related damage.
- Rail Vehicles: Face frequent vibrations during acceleration, braking, turning, and high-speed operation. Wiring systems must withstand fatigue without failure.
2.Resistance to Climate Variations
Transportation systems must perform reliably under extreme temperature and humidity conditions.
- EV Battery Modules: Generate significant heat during charge-discharge cycles. Wiring components must withstand high temperatures and thermal expansion without degrading. Good heat dissipation improves battery efficiency and longevity.
- Aerospace: Requires wiring components that remain stable despite wide temperature fluctuations.
3.Waterproof and Moisture Resistance
- Battery Modules: Enclosed in waterproof casings, but wiring components must resist moisture penetration or condensation.
- Aerospace: Must withstand humidity and condensation to prevent electrical short circuits and maintain insulation properties.
4.Salt, Oil, and Corrosion Resistance
- EVs and Heavy-Duty Vehicles: Exposed to road salt, chemicals, and oils that can corrode wiring materials. Components must resist chemical and environmental exposure.
- Aerospace: Subject to corrosive fuels, lubricants, and salt spray during operations or storage.
5.Lightweight and High Strength
- Aerospace: Every gram matters for fuel efficiency. Wiring components must be lightweight yet strong to support structural integrity.
- EVs: Must balance durability with weight reduction to enhance vehicle performance and energy efficiency.
6. Electromagnetic Compatibility (EMC)
- Battery Modules: Wiring materials must reduce electromagnetic interference (EMI) to avoid affecting surrounding electronic systems.
- Aerospace: EMC is critical to ensure reliable operation of communication and navigation systems.
7.Fire and Low Smoke Toxicity
In emergencies, wiring components must be flame-retardant and emit minimal toxic fumes to protect passengers and equipment.
As technology and time have progressed, the transportation industry has evolved from steam locomotives and steamships to the era of aviation, automobile assembly lines, hydraulic elevators, high-speed trains, bullet trains, lunar rovers, maglev trains, cargo ships, hybrid vehicles, electric cars, autonomous vehicles, unmanned transportation, electric aircraft, hydrogen-powered vehicles, and urban air mobility systems.
To ensure the reliability and safety of wiring systems in these increasingly advanced and demanding environments, efficient and stable wiring management solutions are essential. Products such as steel barb cable ties and stainless steel cable ties play a critical role in securing cables under harsh operational conditions, minimizing failure risks, and enhancing the long-term stability of transportation systems.
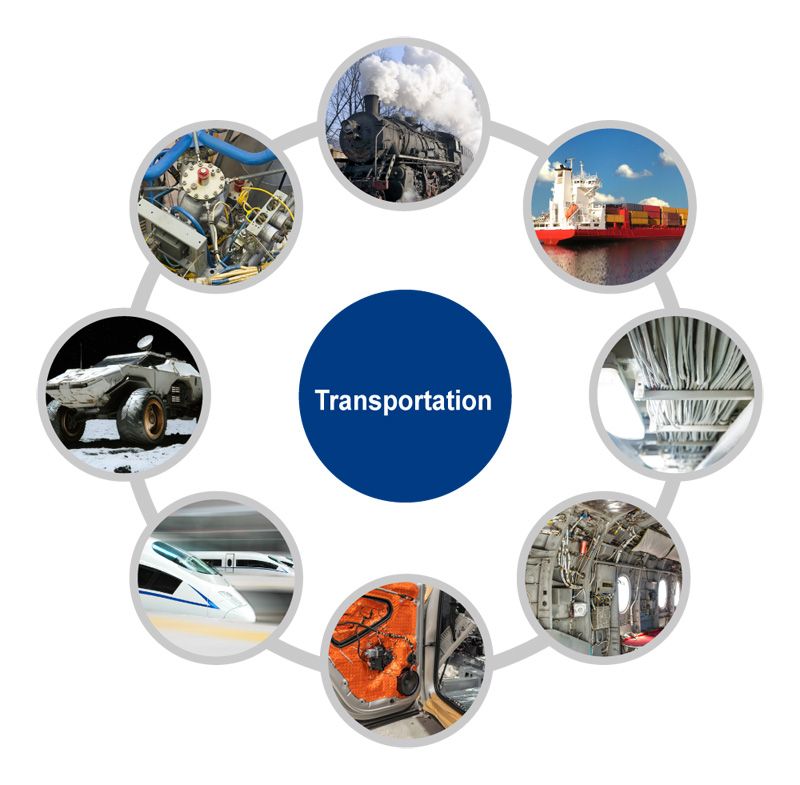
Recommended Wiring Management Components for Transportation
Product Illustration | Applications |
![]() Anti-Vibration Cable Ties/ Steel Barb Cable Ties (View Product Link) | The invention of steel barb cable ties originated from the need for lightweight solutions in the aerospace industry. Traditional bundling methods, which used twine and intricate tying processes, were replaced with nylon plastic ties. To address the weaknesses of fully plastic designs, a stainless steel barb was incorporated into the tie's locking mechanism, providing enhanced fastening and precise positioning compared to plastic components. Fully plastic nylon ties are prone to damage or breakage at their vulnerable locking section under frequent vibration, which can cause the tie to loosen and the bundled wires to unravel. Loose wires not only generate abnormal noise during vehicle operation - particularly in premium or noise-sensitive designs - but also raise concerns about the quality of the vehicle or equipment. Furthermore, loose wires subjected to continuous vibration or friction can lead to insulation wear, exposing the conductor and causing short circuits, electrical instability, or even risks such as failures, malfunctions, and fires. In modern transportation systems, such as autonomous vehicles or trains, loose wires can disrupt communication between sensors and control units, leading to malfunctions in automated systems. For precision-critical control systems, loose wires affect signal accuracy, while unstable power delivery impacts the performance of electric or hybrid vehicles, causing inconsistent power output. As transportation technology advances, steel barb cable ties ensure reliable wire management across applications from aerospace to smart transportation, maintaining stability and preventing failures in demanding operational environments. |
![]() Stainless Steel Cable Ties (View Product Link) | Designed for cable fastening in high-vibration environments, such as undercarriages of railway vehicles and inside aircraft wings. Ideal for applications requiring long-term exposure to salt spray, including ships and harbor equipment. |
![]() Adhesive-Backed Cable Tie Mounts (View Product Link) | Designed for securing cables within vehicle doors or in confined spaces. |
![]() Edge Clip Cable Tie Mounts (View Product Link) | Secures cables to vehicle compartment walls or frames, while protecting shipboard cables from vibration-related damage. |
![]() Flexible Conduits (View Product Link) | Protects cables from abrasion and temperature fluctuations while shielding against electromagnetic interference (EMI). |
![]() Wrapping Bands (View Product Link) | Designed to protect cables around engines and suitable for bundling wires in automotive engines and hydraulic systems, preventing material degradation from oil exposure. |
Learn more about the features and advantages of anti-vibration cable ties/steel barb cable ties , or contact us for additional information.
Why Choose Hua Wei?
- Over 45 years experiences in designing and manufacturing of cable ties.
- Core technology: Precise stamping and molding injection.
- Rich experience and specialty of precise molding in engineering plastic Polyamide 6,6
- Advanced molding facilities and outstanding R&D teamwork
- Our in-house molding capability allows great flexibility in production and enables us to develop products collaboration with our clients.
- Providing customize packaging design and work in process with your brand.
- Stable supply chain with on-time delivery.
Remarks: Hua Wei is a professional OEM factory, followed the MOQ for each order.
New Product
Featured product
Hot
Stainless Steel Ties
Hot
Stainless Steel Ties
With high resistance to various corrosive agents such as acids, alkali, UV, and rust, …
Read MoreHot
Wire Ducts
Hot
Wire Ducts
The premium solution for routing and hiding wires in control panels.
Read MoreHot
Standard Cable Ties
Hot
Standard Cable Ties
Available materials include heat stabilized, weather resistant and flame retardant polymers,...
Read MoreHot
(GIT-703) Cable Tie Tensioning Tool
Hot
(GIT-703) Cable Tie Tensioning Tool
The new cable tie installation tool can fasten and cut nylon cable ties quickly & safely
Read More