Why Choose Steel Barb Cable Ties? Key Differences Compared to Nylon and Stainless Steel Cable Ties
The Story Behind the Innovation
The development of cable ties dates back to the post-World War II era in 1945 when the aerospace industry began to thrive due to the rise of military aircraft. At the time, the vast and intricate wire harnesses in aircraft were traditionally bundled using twine, which was secured by applying wax and reinforced with metal rings. However, this method was far from scientific. Wax-treated twine presented a fire hazard, and the natural twine itself was prone to mold caused by condensation from the temperature differences between atmospheric conditions and the aircraft's interior.
![]() | Moreover, the traditional method made wire harnesses thick and heavy, while laborers who spent days bundling wires suffered from friction burns, bleeding hands, and thick calluses. By the 1960s, to meet the growing demands of the aerospace industry, more scientific wire management solutions were developed. This led to the invention of nylon cable ties, which replaced twine. However, to address the high-performance requirements of the aerospace sector, a critical innovation was introduced: a stainless-steel locking mechanism embedded in the cable tie's tongue. The significance of this stainless-steel piece cannot be understated. Aircraft endure tremendous vibrations caused by aerodynamic forces during takeoff, flight, and landing. The design of the cable ties must withstand these forces to prevent wire harnesses from loosening, which could otherwise pose severe electrical risks. |
Key Advantages of Steel Barb Cable Ties
1. Precision Locking Mechanism
Stainless Steel Locking: The stainless-steel tooth allows the tie to lock securely at any position along the smooth tie body.
Difference with Nylon: Plastic-tooth ties rely on notches along the tie body for locking. This limits the locking position to specific intervals, creating gaps between the tie and the bundled object.
Application: Industries requiring high precision, such as aerospace, automotive, AI, and automated machinery, benefit from the smooth design and precise locking of steel-tooth cable ties.
2. Vibration Resistance
The stainless-steel locking mechanism maintains stability under high-frequency vibrations, acceleration, and aerodynamic forces, ensuring long-term durability.
Plastic Limitation: Plastic locking mechanisms are prone to wear and breakage under constant movement, causing loosening or failure.
3. Resistance to Extreme Climate Conditions
Stainless steel can withstand extreme temperature fluctuations, maintaining strength and stability in both low and high-temperature environments.
It is also resistant to UV radiation, ensuring that its structure remains unchanged even after prolonged exposure to intense sunlight or harsh outdoor conditions.
Plastic Limitation: Nylon or polyester ties soften, deform, or crack in high temperatures, and they become brittle and prone to breaking in extremely low temperatures. Exposure to UV rays accelerates their degradation.
4. Moisture Resistance
Stainless-steel locking components offer exceptional resistance to humidity, preventing corrosion in salt-laden and high-moisture environments.
5. Salt Spray, Oil, and Corrosion Resistance
Stainless steel barb are highly resistant to salt spray, lubricants, and corrosive chemicals, which are common in aerospace, marine, and industrial applications.
According to ASTM B117 testing standards, stainless steel ties can endure hundreds of hours in salt spray environments.
Limitations of Stainless Steel Cable Ties
While stainless steel cable ties offer significant advantages, they do have limitations in certain applications:
1.Cost Constraints
Stainless steel cable ties are 14-20 times more expensive than standard plastic ties. However, their durability and low maintenance requirements make them more cost-effective for long-term use.
Plastic Alternative: Plastic ties are a more economical choice for short-term applications requiring frequent replacements.
2.Weight Sensitivity
Stainless steel ties are heavier than plastic ties, which may negatively impact weight-sensitive applications, such as UAVs (drones) or lightweight aerospace equipment.
Solution: Plastic ties or lightweight bundling materials can be used for applications prioritizing weight reduction.
3.Electrical Conductivity
Stainless steel is conductive and can create risks of electrical shorts, leakage, or electromagnetic interference when directly in contact with live cables.
Solution: In insulated environments, plastic ties or insulated coatings on steel ties are recommended.
4.Flexibility Requirements
Stainless steel ties are rigid and less flexible, making them unsuitable for applications requiring frequent adjustments or fine-tuned positioning in tight spaces.
Alternative: Plastic ties or flexible wrapping bands are better suited for these scenarios.
5.Aesthetic Considerations
The industrial appearance of stainless steel may not meet the aesthetic standards of applications like interior design, home electronics, or decorative environments.
Solution: Plastic ties with clean and polished finishes are better suited for such uses.
6.Installation Safety
Stainless steel ties require specialized tools for tightening and cutting, and the sharp edges left after cutting can pose safety risks to workers.
Solution: Plastic ties are safer and easier for manual installation, especially in temporary or high-labor environments.
Although stainless steel cable ties offer exceptional strength, durability, and corrosion resistance, they have limitations in terms of conductivity, weight, flexibility, cost, and certain chemical or operational environments. Selecting the appropriate cable tie material and design based on actual application requirements is essential to achieve the optimal balance of safety, cost-effectiveness, and practicality.
Suitability of Plastic Materials
While plastic materials are low-cost and lightweight, their performance is limited under harsh conditions, making them suitable for short-term or non-extreme environments. In the following situations, fully plastic materials may have disadvantages:
1. High-Temperature, Low-Temperature, or UV Exposure Environments
Plastic materials have limited resistance to high temperatures. Prolonged exposure to heat can cause melting, deformation, or performance degradation. In extremely low temperatures, plastics may become brittle, lose flexibility, and easily fracture. Furthermore, UV radiation accelerates aging, causing the material to deteriorate, discolor, or crack when exposed to sunlight over long periods.
2.High-Load Environments
Plastics have lower tensile strength and rigidity, making them unsuitable for applications requiring sustained high loads or heavy pressure. In structural support components of large machinery or for heavy cable management under constant high tension, plastics are weaker than metals and may undergo permanent deformation over time.
3.Chemically Corrosive Environments
General plastic materials can degrade, corrode, or dissolve when exposed to acids, alkalis, solvents, or other chemicals. This makes them unsuitable for applications in chemical plants, laboratories, or other highly corrosive environments.
4.Salt Spray or High-Humidity Environments
Certain plastics (such as nylon) absorb moisture, which can penetrate the microstructure of the material, altering its physical properties and causing swelling, deformation, or reduced mechanical strength. Additionally, plastics tend to age over time, leading to performance degradation, brittleness, and cracking. This makes them less suitable for environments such as marine applications, port equipment, or areas with high salt spray and humidity.
5.High-Wear Environments
Plastics have lower abrasion resistance compared to metal materials. In high-wear or frequent-contact applications, plastics may wear out quickly due to friction. For example, components in industrial machinery that frequently contact metal parts are prone to rapid wear.
Plastic materials are lightweight, highly flexible, durable, and easy to process, offering significant economic benefits in cost control. Furthermore, they provide excellent electrical insulation, making them suitable for a wide range of environmental conditions. Plastics are particularly advantageous in applications that require flexibility and design versatility.
However, plastic materials face limitations in extreme environments, such as high or low temperatures, heavy loads, and corrosive conditions, as well as in maintaining long-term performance and stability.
The Innovation of Steel Barb Cable Ties
Steel barb cable ties bridge the gap between the advantages of stainless steel and plastic ties, particularly for aerospace applications that demand lightweight, stable, and weather-resistant solutions.
Key Features of Steel Barb Cable Tie Design
1. Plastic Body with Stainless Steel Tongue
Combines the flexibility, light weight, and insulation properties of plastic with the durability, vibration resistance, and precision locking of stainless steel.
2. Ergonomic Design
Rounded head design reduces worker fatigue and minimizes friction during installation.
3. Solid Tie Body with Anti-Slip Features
Unlike traditional notched designs, the smooth, solid body prevents stress concentration and ensures no bite marks on bundled items. Raised patterns and ribs enhance grip and prevent sliding under vibration.
4. Tail Design
The extended, ergonomic tail allows for easy installation in confined or blind spaces.
5. Enhanced Grip Points
Special grip surfaces make installation easier, even when wearing gloves or working in wet and cold conditions.
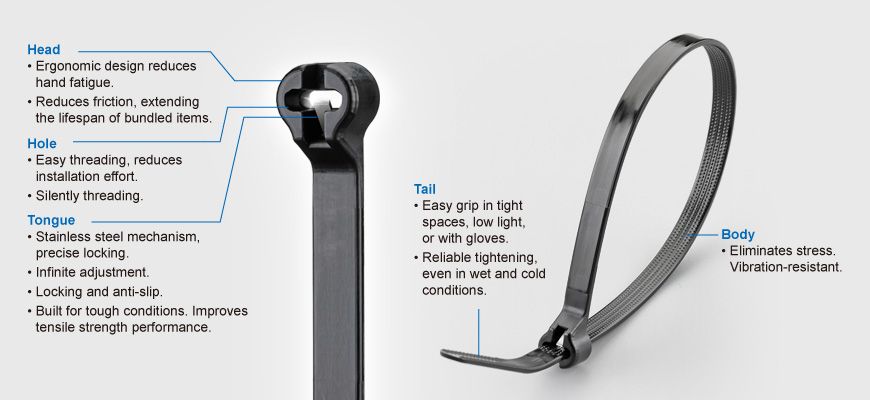
Steel barb cable ties were designed to address the challenges of traditional bundling methods in the aerospace industry, reducing worker fatigue, lowering aircraft weight, and improving safety. Over time, their design principles have expanded into automated machinery, drones, and emerging transportation technologies. While their cost is 2-3 times higher than traditional nylon ties, they remain the preferred choice for industries requiring stability, precision, and reliability under extreme conditions.
![]() |
![]() |
![]() |
![]() |
Automation | Transportation | Shipbuilding | Home Theater |
Steel barb cable ties bridge the gap between nylon and stainless steel ties, offering:
1. Precision locking for high accuracy.
2. Superior vibration resistance for dynamic environments.
3. Extreme climate and corrosion resistance for harsh applications.
4. Lightweight design for weight-sensitive uses.
This makes them the preferred solution for industries requiring stability, reliability, and long-term performance, such as aerospace, automotive, automation, and marine applications. While their cost may be higher than traditional nylon ties, their unmatched performance and durability provide significant value in demanding conditions.
Read more articles about Steel Barb Cable Ties
Download the Steel Barb Cable Ties catalog
Download the Nylon Cable Ties catalog
Download the Stainless Steel Cable Ties catalog
Contact us to determine the most suitable cable tie solution.
New Product
Featured product
Hot
Stainless Steel Ties
Hot
Stainless Steel Ties
With high resistance to various corrosive agents such as acids, alkali, UV, and rust, …
Read MoreHot
Wire Ducts
Hot
Wire Ducts
The premium solution for routing and hiding wires in control panels.
Read MoreHot
Standard Cable Ties
Hot
Standard Cable Ties
Available materials include heat stabilized, weather resistant and flame retardant polymers,...
Read MoreHot
(GIT-703) Cable Tie Tensioning Tool
Hot
(GIT-703) Cable Tie Tensioning Tool
The new cable tie installation tool can fasten and cut nylon cable ties quickly & safely
Read More